
「機械にはできない職人芸から生まれるもの」
vol.8第一ゴム株式会社 営業部長・村上孝之さん/小樽市
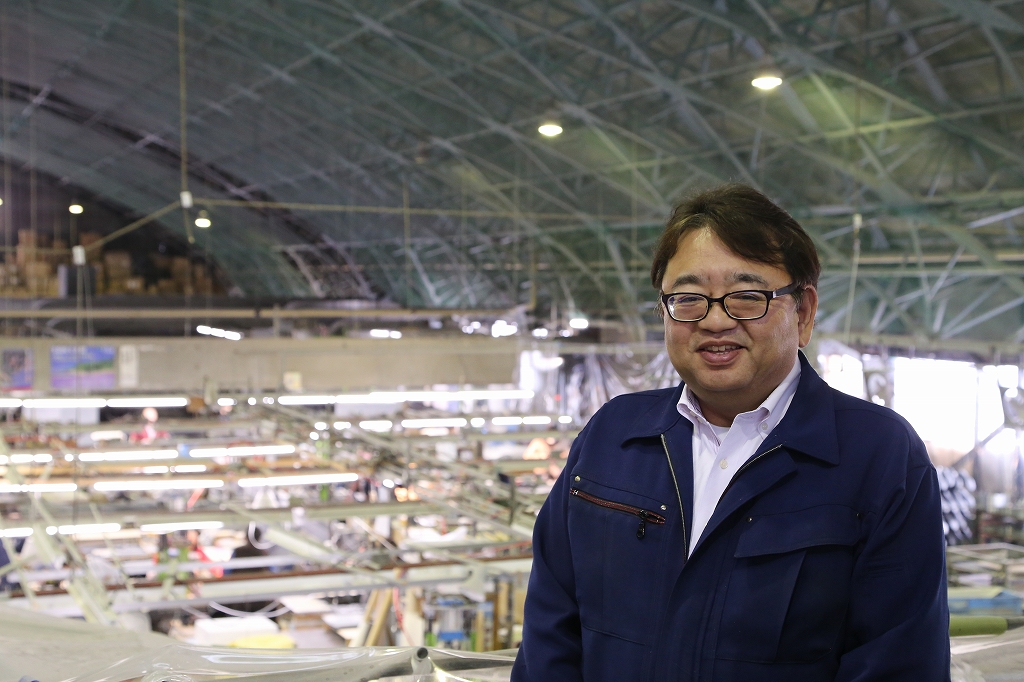
1950(昭和25)年、港まち小樽には16もの中小ゴム工場が稼働していたという。
現在、海外で長靴を生産するメーカーが多い中で、創業83年の第一ゴムは、いまも国産にこだわり、北海道ならではの「滑らない長靴」を生産し続けている。

北海道のゴム工業は小樽からはじまった
1909(明治42)年、イギリス企業のダンロップが日本初のタイヤ工場を設立したのは、外国との貿易が盛んな神戸だった。小樽の場合、ゴムに目をつけたのは富山の繊維問屋である。地下足袋の底にゴムの滑り止めを付けるという発想からはじまった。1917(大正6)年、北海道護謨工業合資会社(現・ミツウマ)が設立、3年後からゴム靴の生産・修理を開始した。
第一ゴムの創業者、濱村由太郎は石川出身。神戸でゴムの配合を学び、東京の会社に入社してからもセールスマンとして、小樽によく来ていた。ニシン漁をはじめ、石炭の積み出し港として発展し、北海道の経済の中心として繁栄を極めていた小樽に、濱村は確かな可能性を感じたに違いない。1935(昭和10)年、新興化学合資会社(現・第一ゴム)を設立。昭和初期は北海道のゴム工業が波に乗り始め、販売ルートも道内外へと広がっていた時期でもある。物資不足となった戦後も、濱村の再生ゴムを利用するアイデアと技術で切り抜けたという。
現在、道内で唯一、国産の長靴を生産し続けている第一ゴムは、創業当初と変わらない奥沢町にある。小樽市街地を流れる勝納(かつない)川の上流にあり、大正時代から水源地が整備され、電動機械が普及する前は、水車が大型ローラーの原動力だったという。かつては第一ゴムやミツウマのほか、三興ゴム、北辰ゴム、日成ゴム、北海ゴムなど、数多くのゴム工場が建ち並び、全社で3000人もの従業員が働く地域だった。「最盛期の1965(昭和40)年頃、うちも500人ほどの従業員がいました。僕らが子どもの頃は、短靴もゴム製だった時代ですからね」と、営業部長の村上孝之さん。
第一ゴムのセールスポイントは、冬の坂道でも滑りにくい長靴に力を入れていること。「道内企業だからこそ、7、8割の開発費を冬物に投じられる」という。中でもゴムにセラミックを混ぜ込んだ靴底にスチールピンを埋め込んだダブルスパイクは、24年前に開発された最強の靴底。気温が緩んで溶けた雪が、急な冷え込みでスケートリンクのように凍る路面、さらに一見アスファルトが濡れただけのようで、薄い氷の膜が張る「ブラックアイスバーン」の恐ろしさは、北海道人なら誰もが実感している。
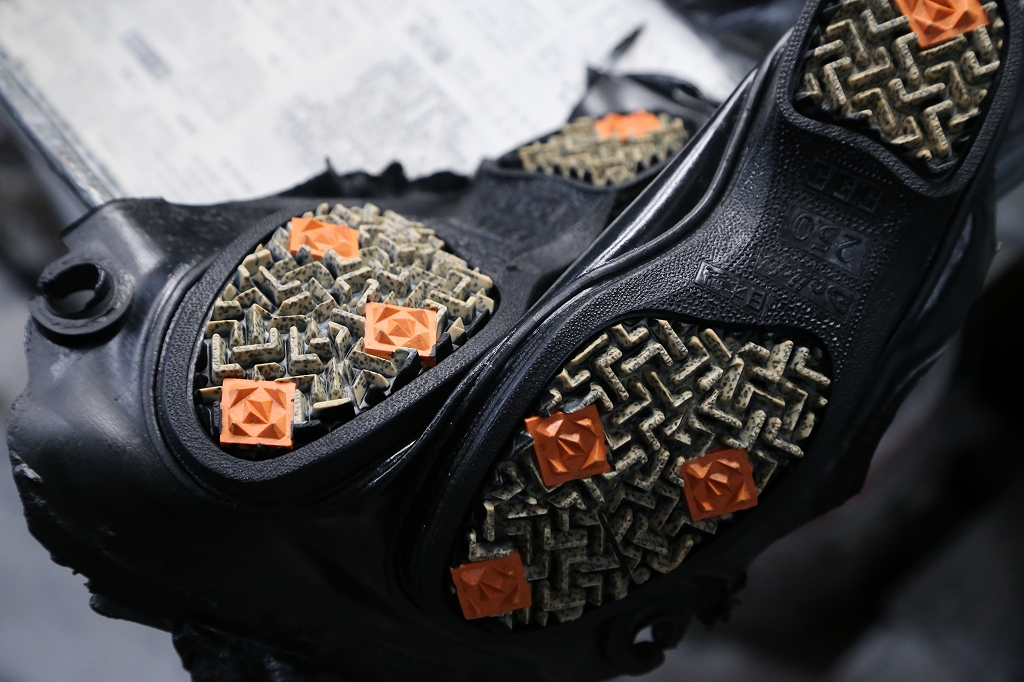
碍子を細かく砕いたセラミック入りの靴底に、オレンジのゴムでカバーしたスチールピンを埋め込む。スチールピンだけでは床が傷つくという問題を改良したものだ
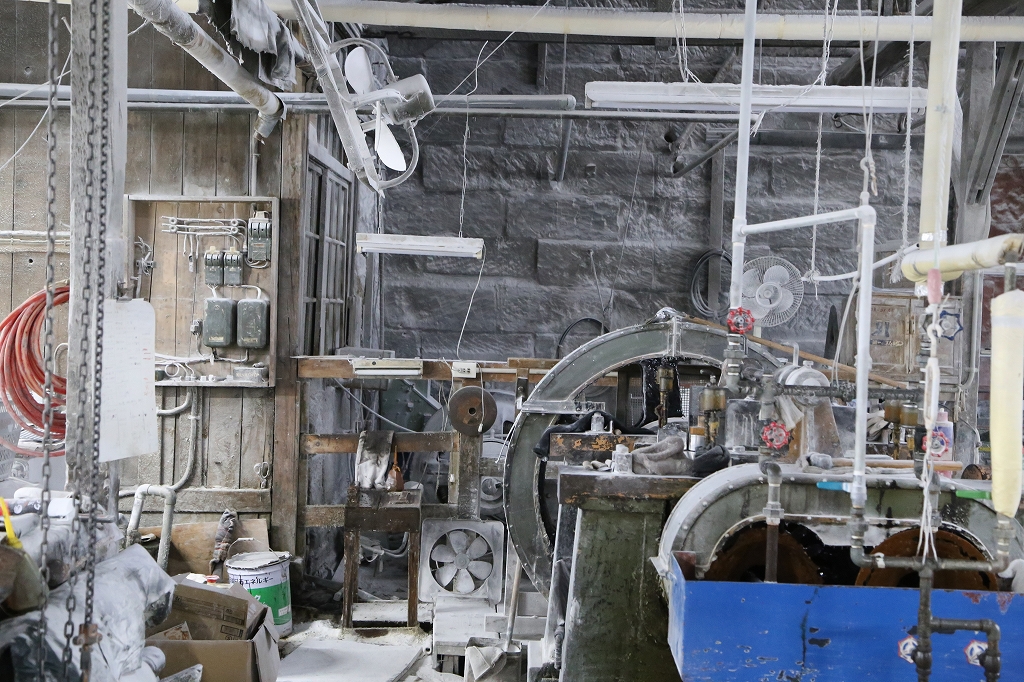
世界遺産の富岡製糸場と同じような三角トラス工法と明り取りのある越屋根、軟石やレンガ壁など、創業当初に建てられた工場も現役で使われ、置かれたすべてのものが歴史を物語る
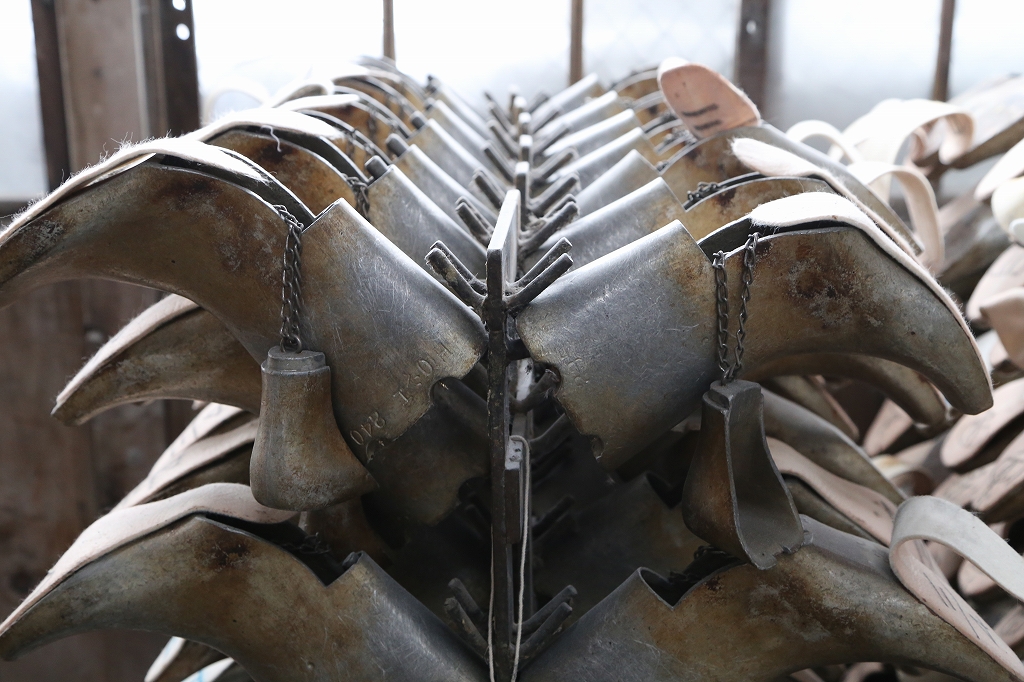
数え切れないほどの金型が山積みに。中には創業当初からの型もあり、昔のジョッキーブーツをモデルしたものは、大手アパレル会社も目を付ける
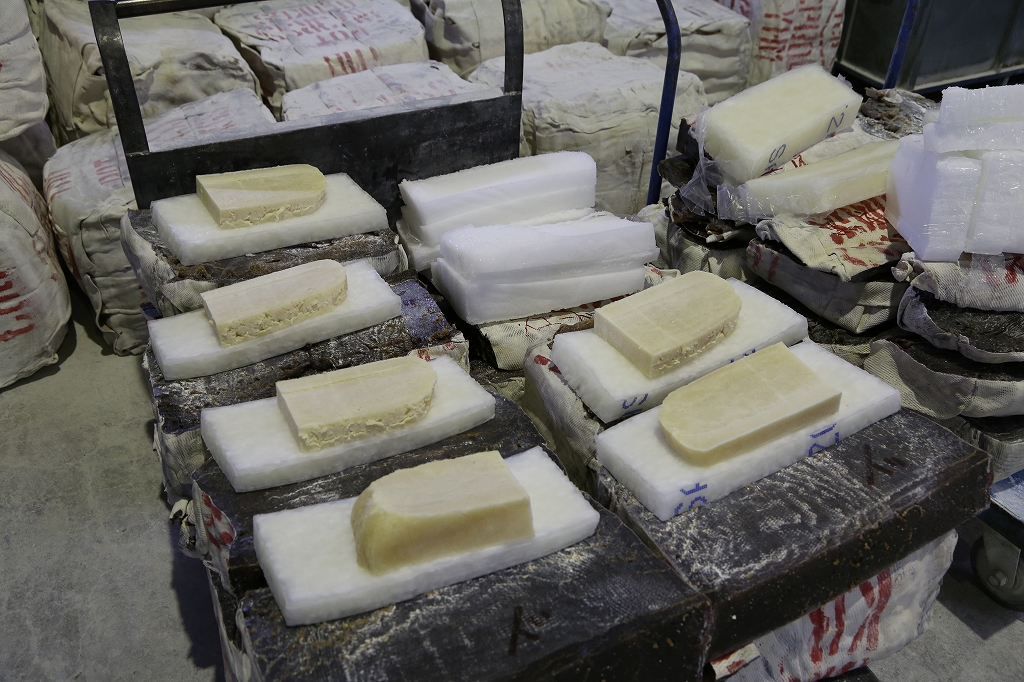
純度の高い良質な天然ゴムは、インドネシアやマレーシアなど東南アジアから輸入。それだけでは軟らか過ぎるため、合成ゴムをつなぎに配合する
この手間が国産の品質を守り続けている
村上さんの案内で、工場内を見学して驚いたことがある。それは、オートメーション化が進んでいるこの時代に、手作業なしでは長靴の生産は不可能だということだ。最新の機械で、ポンポン大量生産されていく姿を想像していたが、まったく逆の職人技が要になっている。「ゴムは生きている。その日の気温や湿度によって伸び具合が変わってくるので、引っ張る力を加減したり、手作業で調整する必要がある。ロボットや機械は一定の力でしか作業できないから、これはまだ人間の力に頼るしかない。それは、道外の大手工場でも、中国の工場でも同じ」という。
長靴が完成するまでの工程を順に説明してみよう。まずは原料を混ぜ合わせゴムを板状にのばしていく。その板状のゴムから、本体、靴底、補強部品、飾り部品など、いくつものパーツを作る。そして本体の内側となる裏地を金型にかぶせ、その上からゴムのパーツを貼っていくのだが、この手作業が、長靴の品質を左右する。「最も難しいのは靴底と本体を貼り合わせる作業。カーブや凹凸がある部分を手繰ったり、きれいにピシッと貼る作業は、繊細な日本人ならでは」。第一ゴムが人件費をかけてでも、国産を守り続けている理由だ。
すべてのパーツを貼り合わせ、検品してから「加硫缶」という装置に入れて、熱と圧力を加える。この工程により弾力のあるゴムに変化し、丈夫で耐久性のある長靴になるのだ。加硫を終えたら、金型を抜き、余分なゴムを切り落とし、仕上げの縫製作業と水漏れ検査を行い完成となる。
2年ほど前から、村上さんは札幌のデパートで開催される「冬靴フェア」で自ら販売員となり、消費者の声を聞くチャンスを得た。「滑らない長靴は60~70歳くらいの高齢者向きだと思っていたが、もっと若い世代、赤ちゃんを抱える若いお母さんたちからの要望が強いことも知った。今後の商品開発にも役立てたい」と意気込む。
第一ゴムは初代の頃から、従業員のアイデアや意見を積極的に商品開発に生かしてきた社風がある。東京や大阪の大手アパレル企業とコラボしてレインブーツを生産したり、農家用に生産している昔ながらの黒い「田植長」が東京の雑貨店でヒット商品になっていることを考えると、未来は明るいと感じさせてくれる道内企業の一つだ。
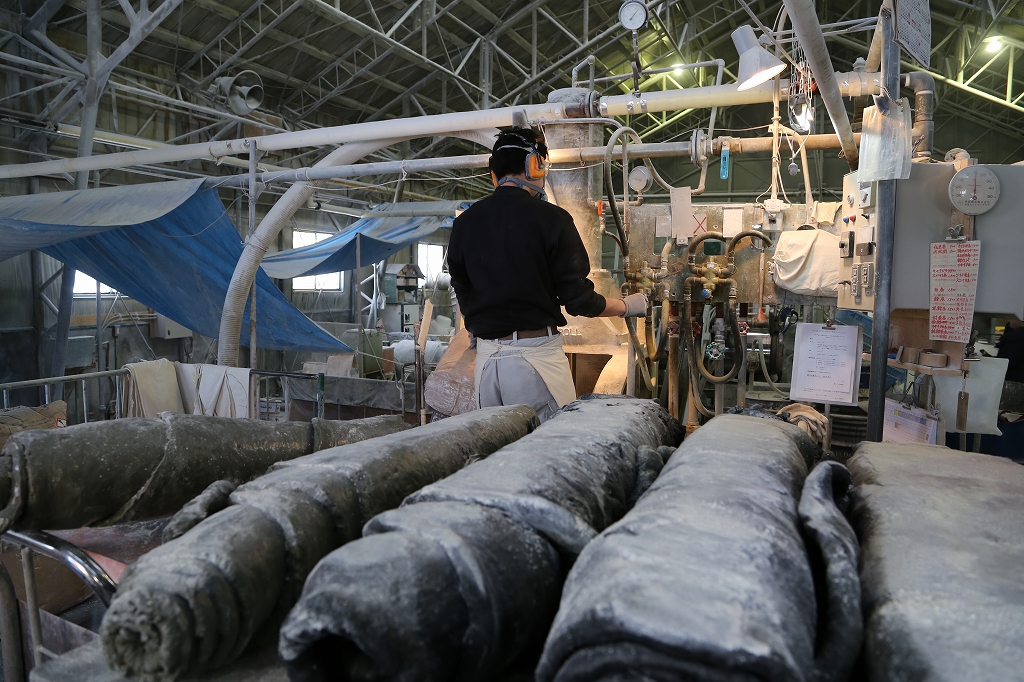
原料のゴムを配合し、パン生地のように練ることから作業ははじまる
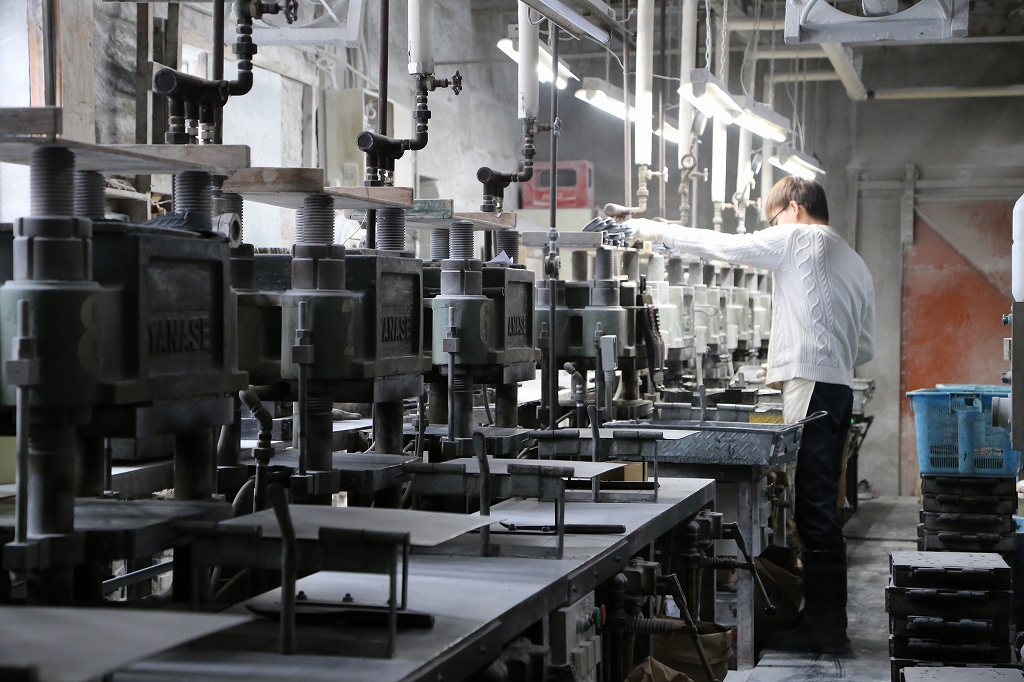
プレス機械でワッフルを焼くように、靴底が出来上がっていく
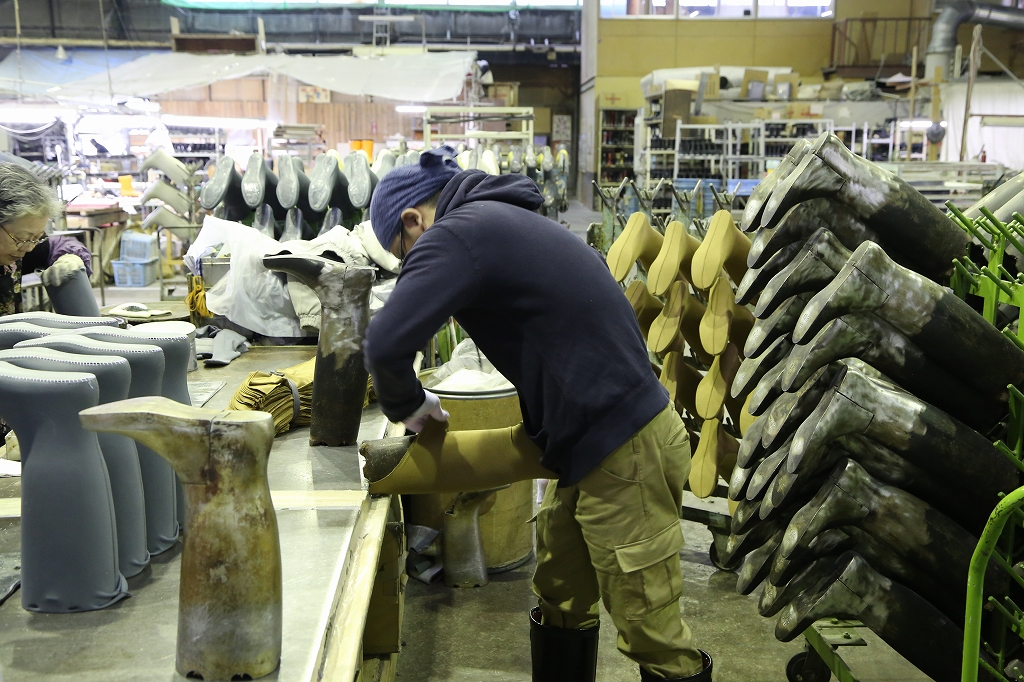
金型にまず裏地をはかせる。夏用は薄いメリアス生地、冬は防寒用のウレタンなどスポンジを使う
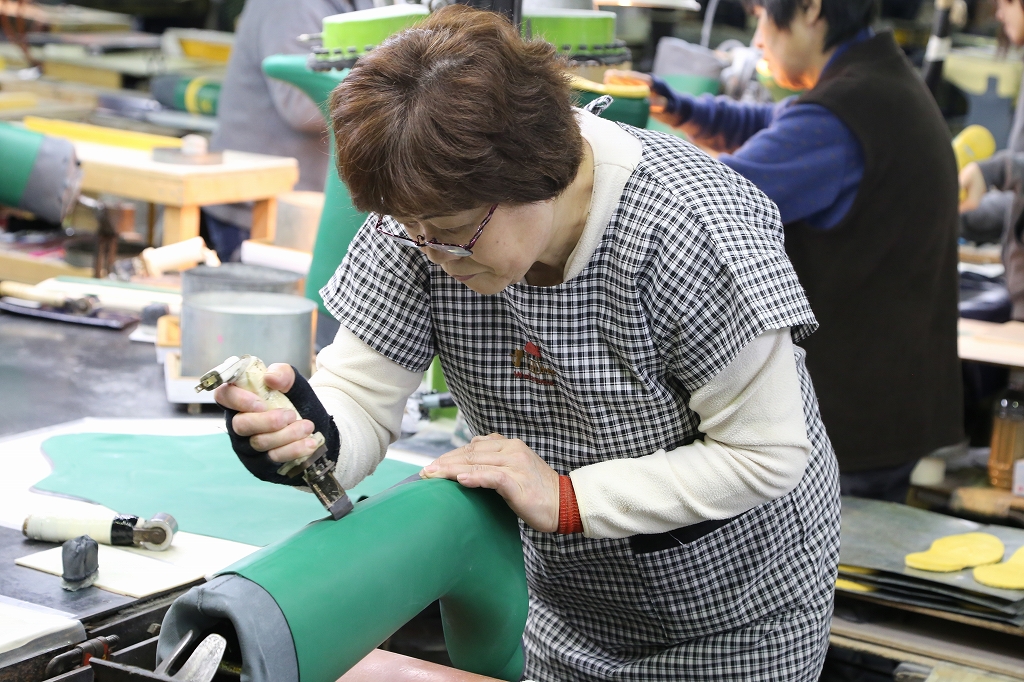
長靴のパーツを貼り合わせる作業はまさに職人技。1足1足ていねいに仕上げていく
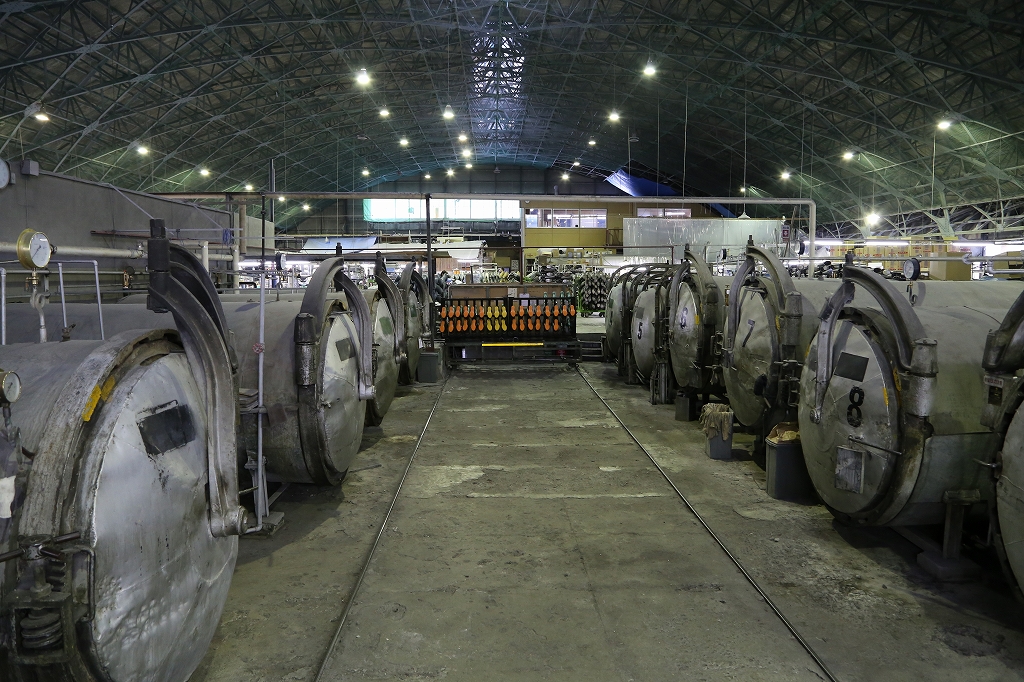
加硫缶の中はサウナのような状態。140℃の熱を1時間加えることでゴムに伸縮性が生まれる
第一ゴム株式会社
北海道小樽市奥沢3丁目29-32
TEL:0134-22-5161
Webサイト